Carbon coated titanium dioxide multi-layer nanostructured electrodes for capacitive deionization
Capacitive deionization technology is a new electrochemical water purification technology with high efficiency, low energy consumption, no secondary pollution and simple operation and maintenance, and can be widely applied in various fields such as water softening, seawater desalination, high value heavy metal ion recovery and groundwater remediation. Unlike the conventional use of carbon nanomaterials as adsorption electrodes, the Center proposes a new concept of capacitive deionization electrode design: the use of anodic treatment and hydrothermal treatment to grow titanium dioxide nanostructures on the surface of titanium foam. Then, glucose is used as the carbon source for high-temperature carbonization, and a carbon film is grown on the surface of the titanium dioxide nanostructure to produce a porous titanium dioxide multilayer nanostructure covered with carbon, so that this electrode has high specific surface area, low interface impedance, high ion transport capacity and high electrochemical stability characteristics. The carbon coated titanium dioxide nanostructured electrode was tested at a voltage of 2 V and an electrode spacing of 125 μm, and the conductivity of aqueous sodium chloride solution could be reduced from 748 to 527 μS/cm.
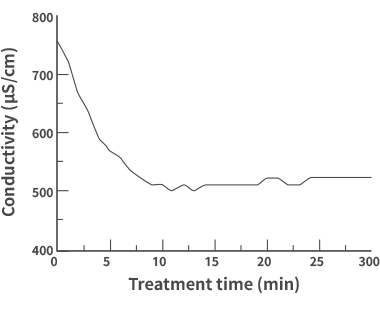
Results of electrosorption equilibrium test with carbon-coated titanium dioxide multilayer nanostructured electrodes at an initial conductivity of 750 μS/cm.
Metallized fabric for collection electrodes of electrostatic collectors
In view of the harmful effects of air pollution on human beings, many air purification technologies have been developed. Among them, electrostatic dust collection uses the interaction between collecting electrodes and electrically charged suspended particles to capture and eliminate PM2.5 and degrade organic hazards (e.g. formaldehyde). In order to achieve the goal of improving the dust removal efficiency, the center innovated the use of airflow sputtering technology to grow silver metal film on sandwich mesh at low temperature and high speed, which can replace the existing heavy stainless steel electrodes by increasing the contact area between charged suspended particles and metallized fabric with high surface area. The dust collection efficiency of metallized fabric as collection electrode is >99% under the test environment of 40 x 40 x 40 cm3 enclosed space, and the CADR value of our own miniaturized electrostatic dust collection is 25 m3/h. Another dust collection test was conducted in an open space of 7.5 ping, and under the condition that the collection electrode has the same viewing area, the metalized fabric can collect different particle sizes. The dust collection efficiency of metallized fabric for different particle sizes is obviously better than that of traditional stainless steel plate, which demonstrates the high performance of electrostatic dust collection. This structure is expected to subvert the structure of existing commercially available devices and achieve the goal of efficient air purification.
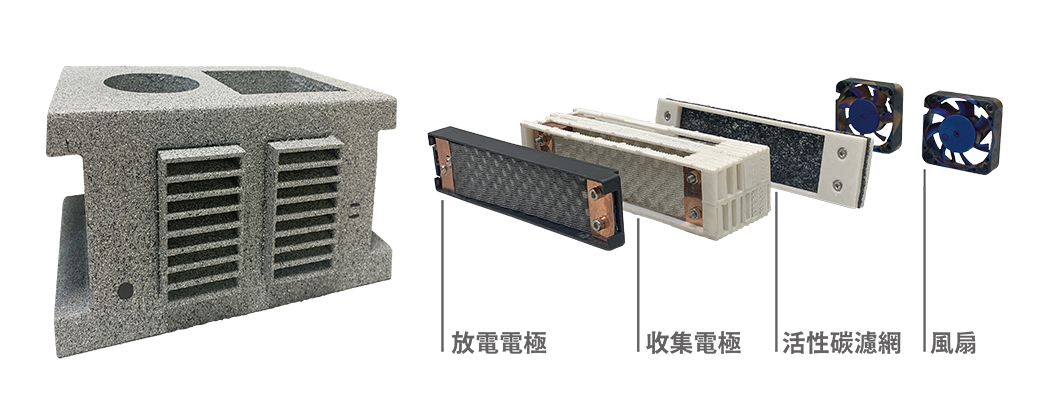
Realistic view of self-made miniaturized electrostatic dust collection device: (left) exterior and (right) interior disassembly.
▲The results of PM2.5 concentrations at different test times under a closed and severe test environment (with wire incense as the source of PM2.5 and its initial concentration > 999 μg/cm3), using metallized fabric as the collection electrode for self-made miniaturized electrostatic dust collection.
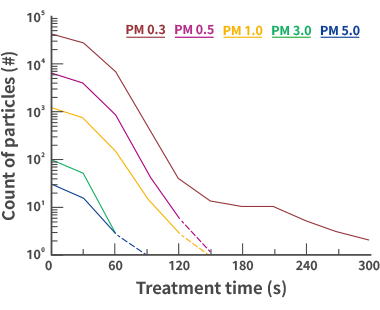
Dust collection test with metalized fabric as self-made miniaturized electrostatic dust collection electrodes under closed normal test environment, particle count results at different test times.
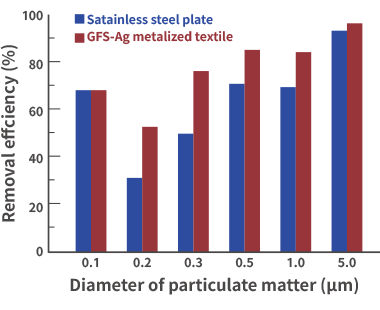
Open test environment, use stainless steel plate and metalized fabric as electrostatic dust collection electrode for dust collection test, dust collection efficiency after 30 minutes of test time.
Green plasma process to grow porous electrode materials for capacitive electrode foil applications
This technology is the result of the joint development of our center and Gem Plasma Technology Co., Ltd.
It is known that electrode aluminum foil is the key material in aluminum electrolytic capacitors because it has the highest material cost and directly determines the electrostatic capacity, so it is the key material with the highest technical content and added value. Although the existing technology of growing porous structures on the surface of electrode aluminum foil by wet electrochemical etching is quite mature, it has given rise to high pollution process and high energy consumption problems. In addition, the high-capacity electrode aluminum foil has been monopolized by Japanese manufacturers for a long time, the growth of electrostatic capacity has reached a plateau, and the production capacity is limited due to the carbon neutral environmental protection policy, etc. Therefore, the key material with high electrostatic capacity can be developed by using green process to stand out in the blue ocean market.In order to achieve this, we propose the process technology of “green plasma process to grow porous electrode material”, which is a groundbreaking innovation. By using air sputtering to grow dense and porous aluminum metal film structure directly on the surface of aluminum foil, we found that the capacitance of this porous material can exceed 4.5 times of traditional wet process. Therefore, for the aluminum electrolytic capacitor industry, it will have a great process substitution and competitive advantage.